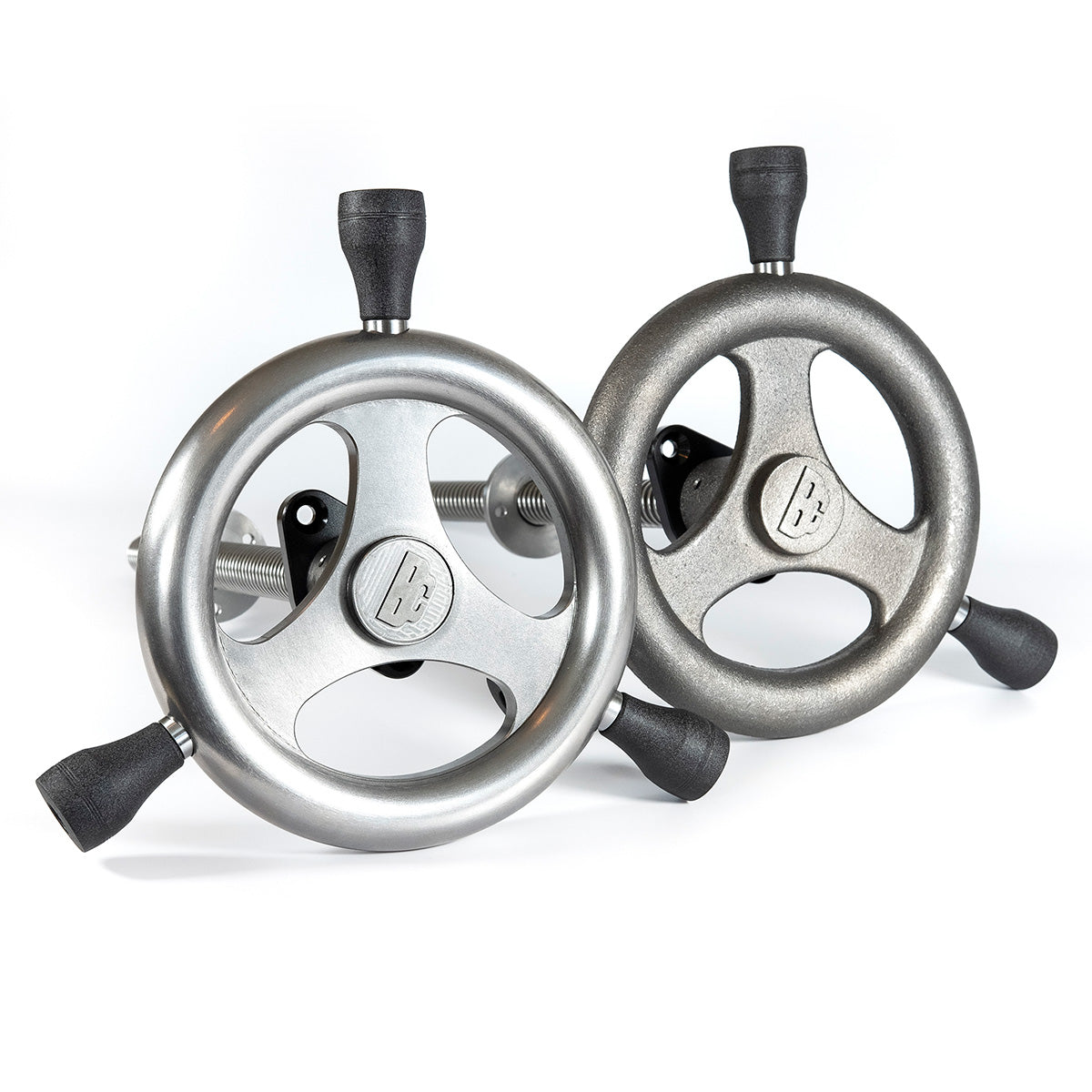
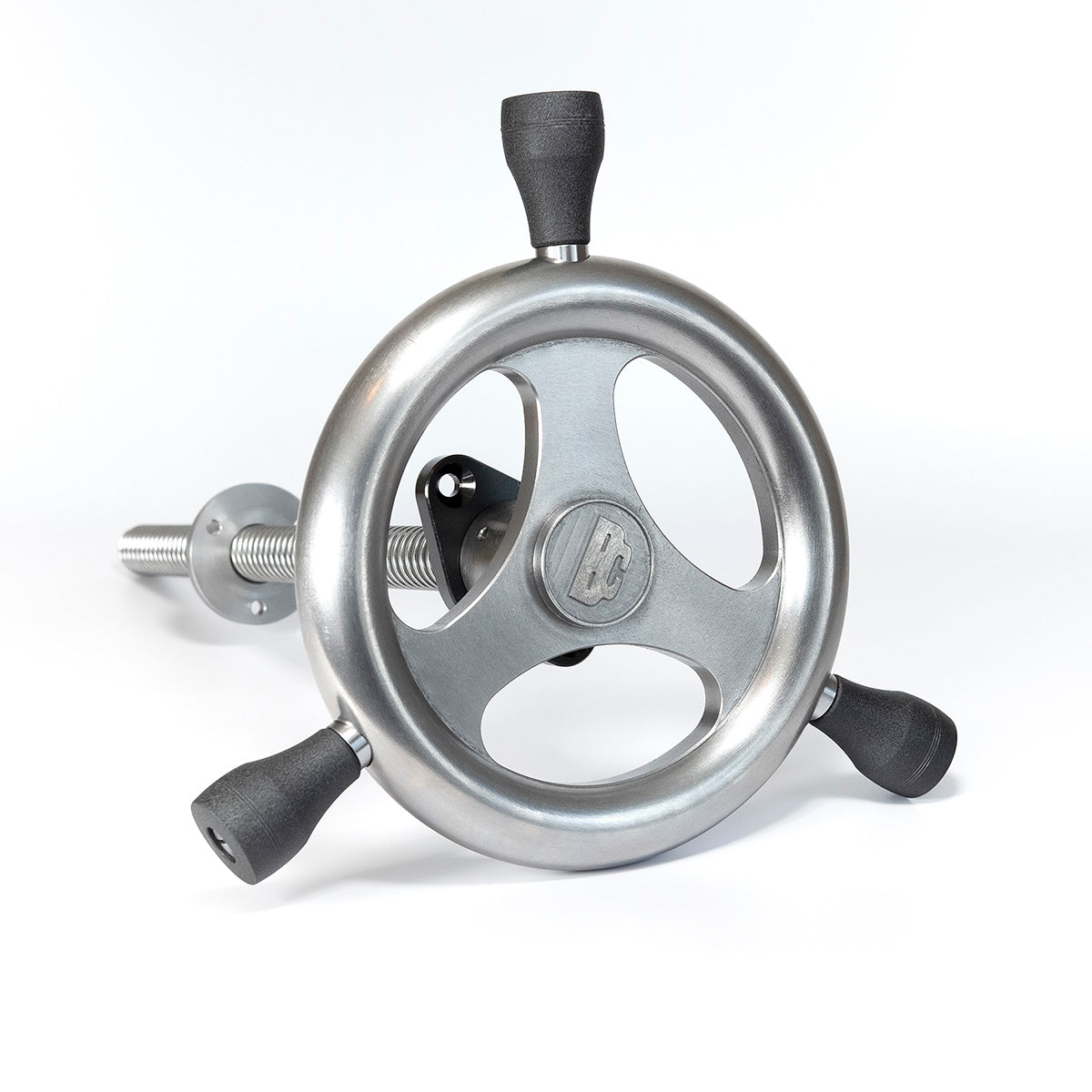
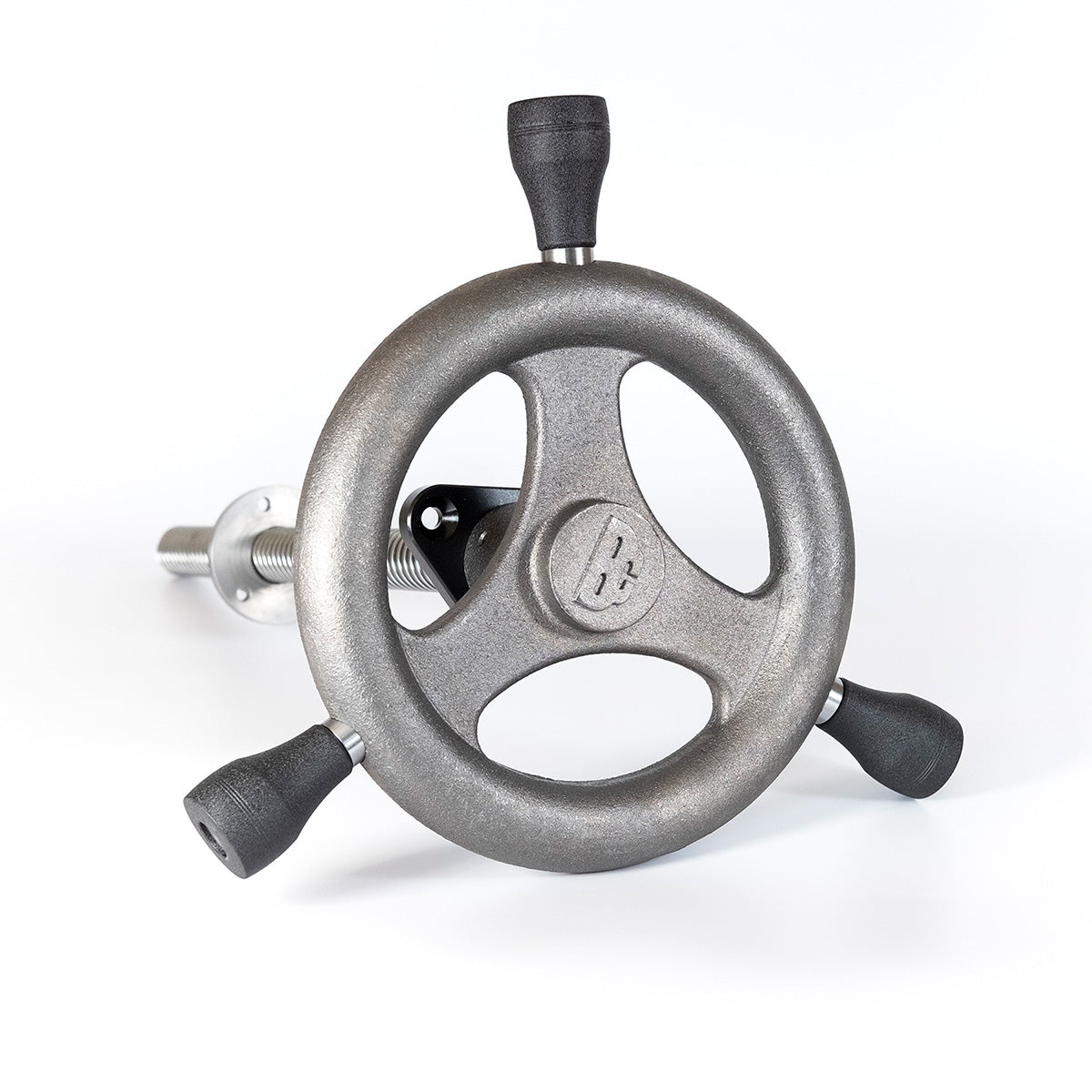
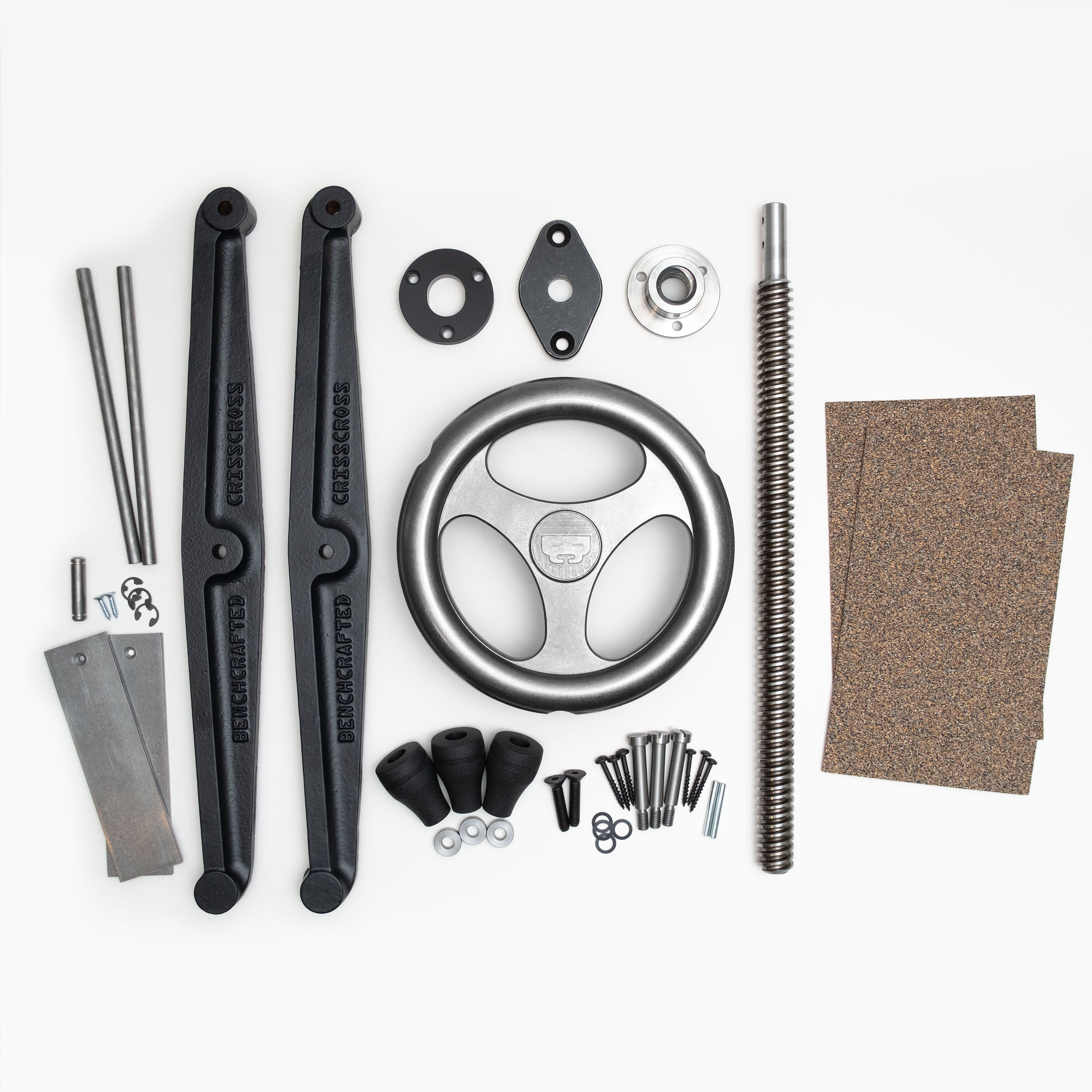
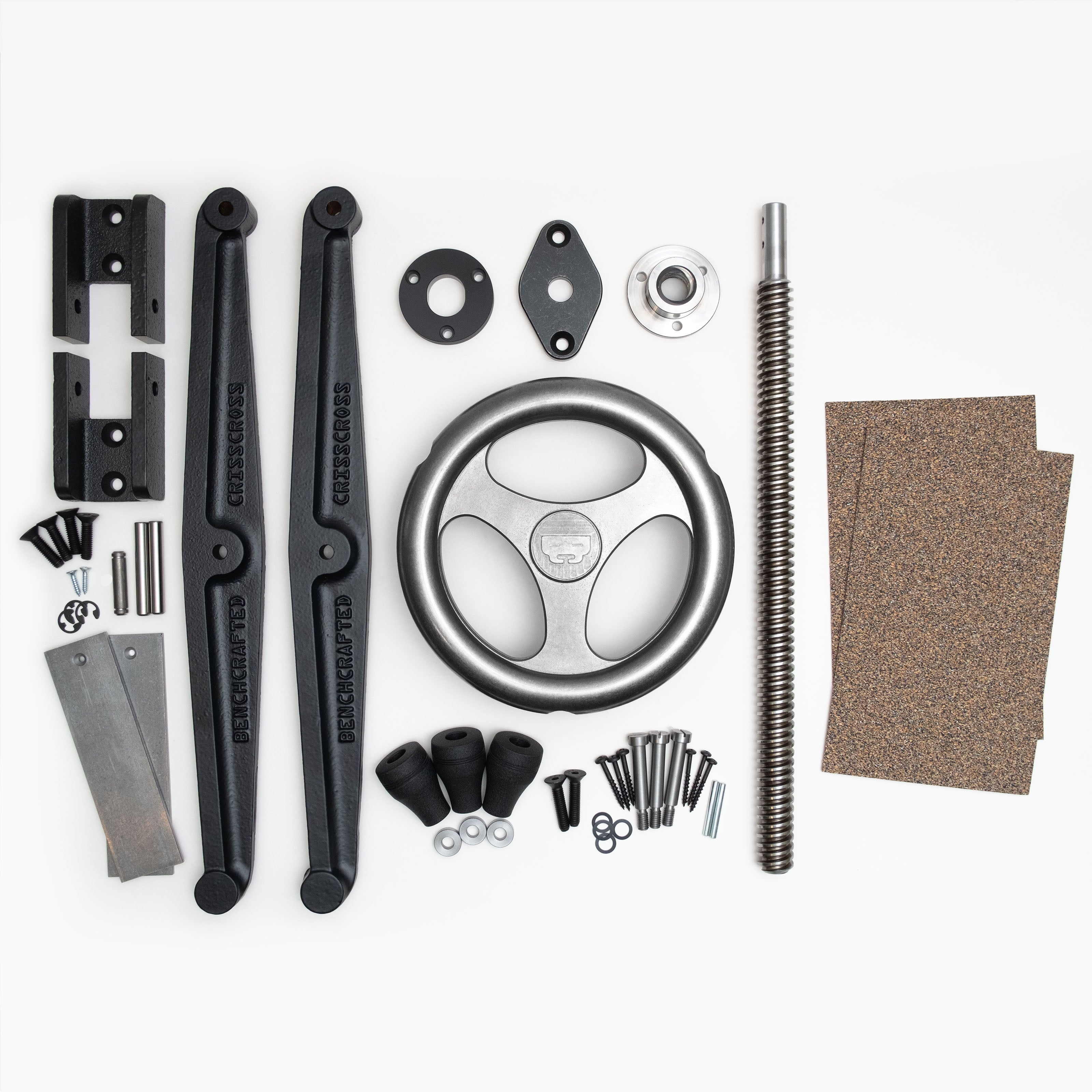
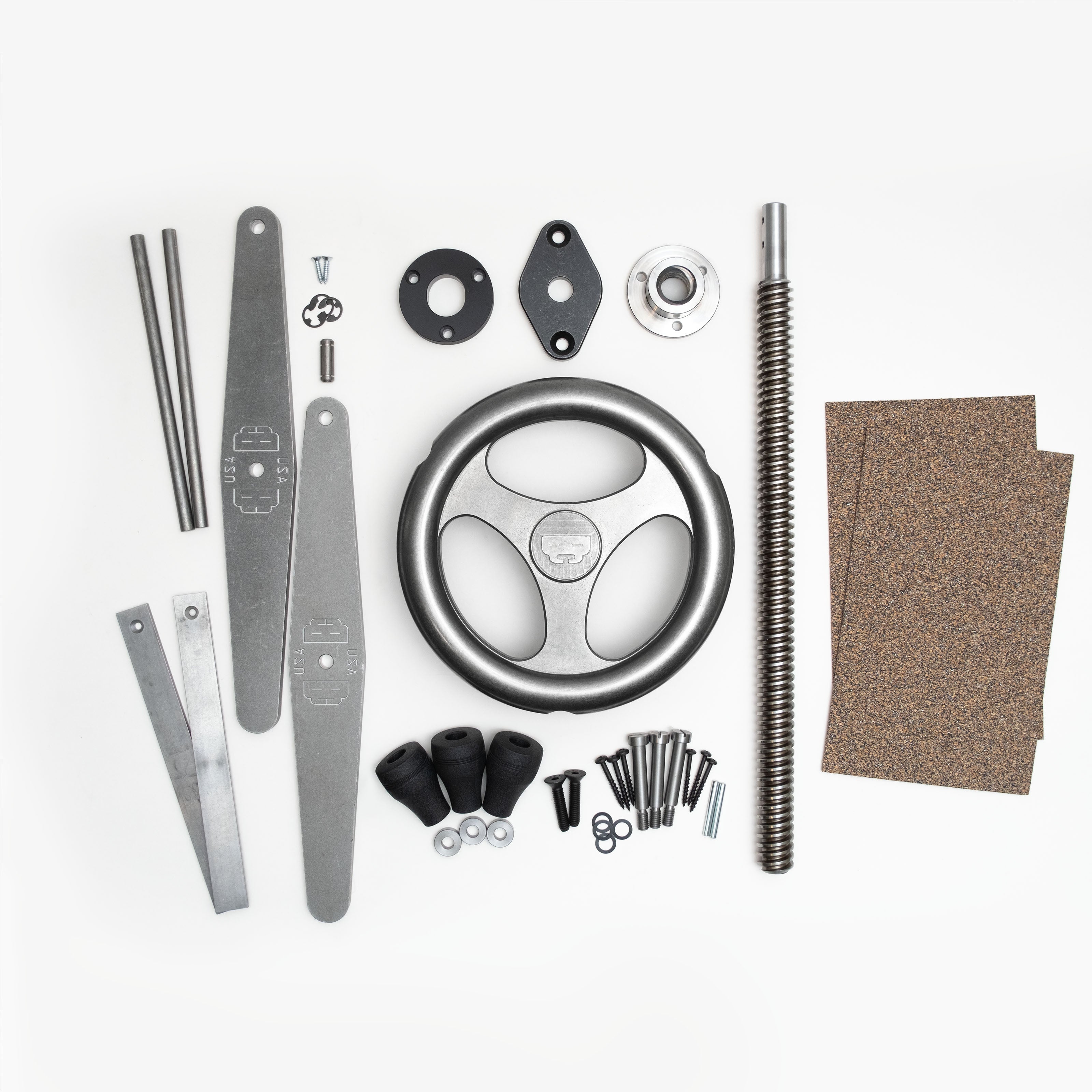
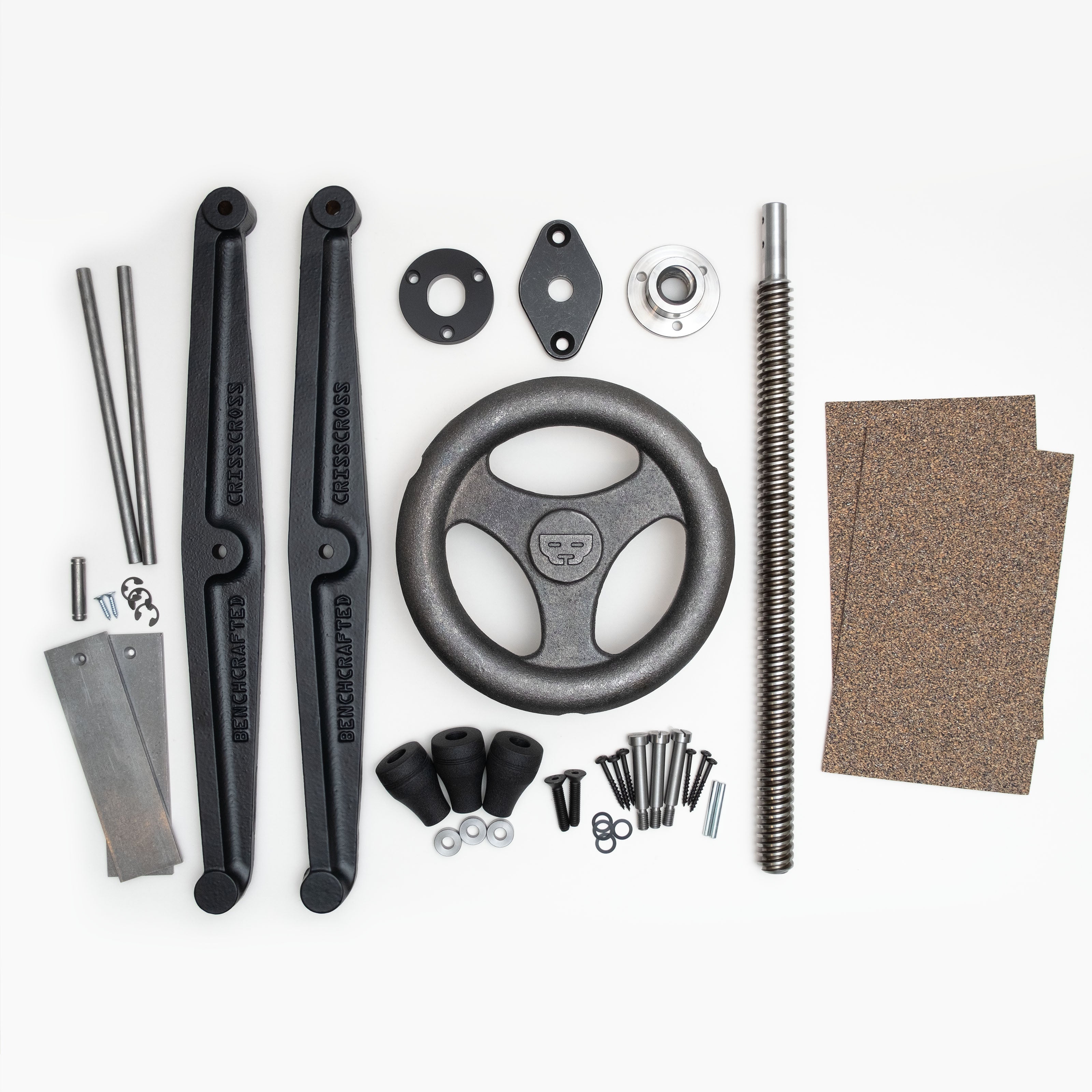
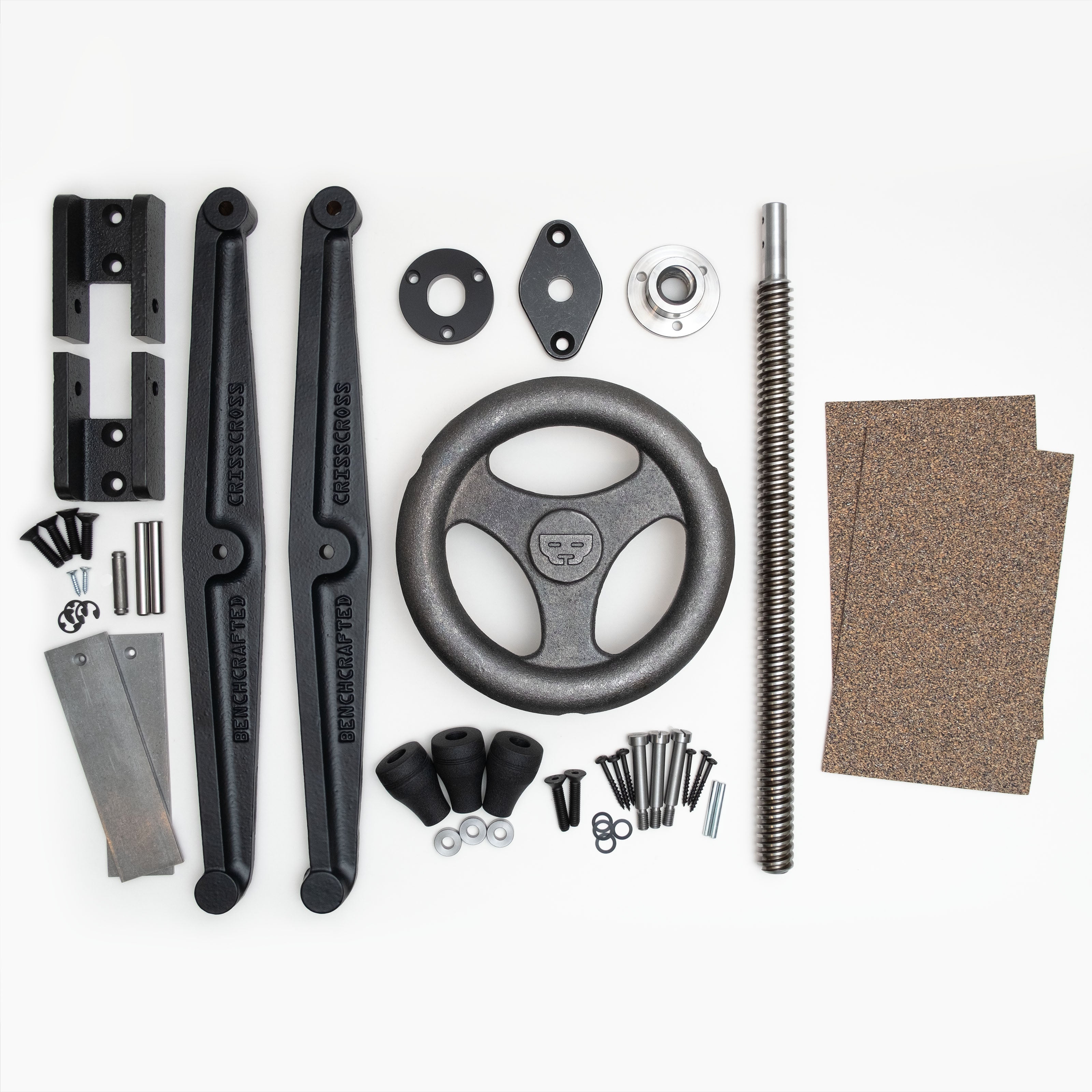
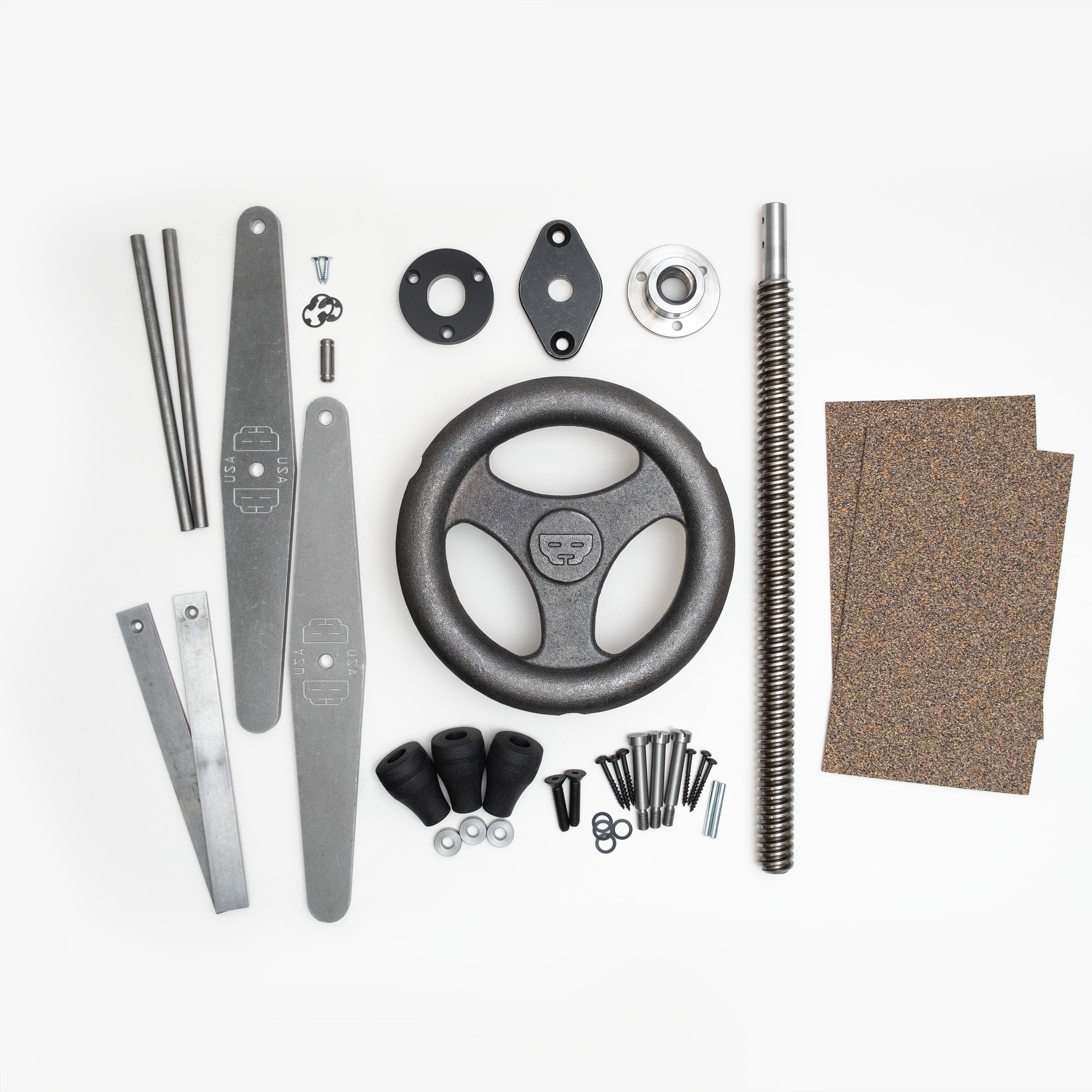
Glide Leg Vise
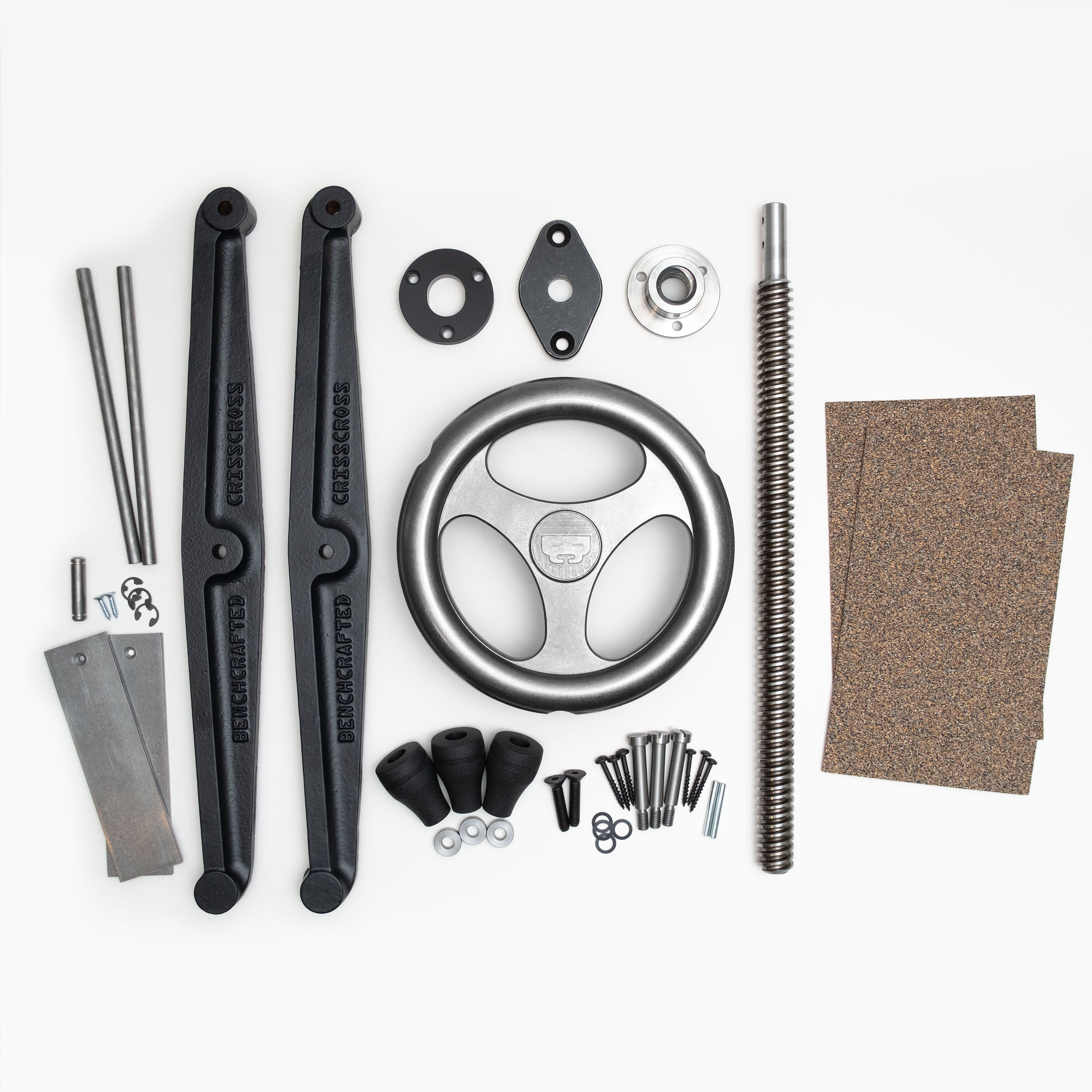
FORM and FUNCTION
The Glide makes holding your work quick, easy, and pleasurable. It uses a clever combination of components to deliver incredible clamping force with minimal effort. The Glide exemplifies our principle of effortless workholding.
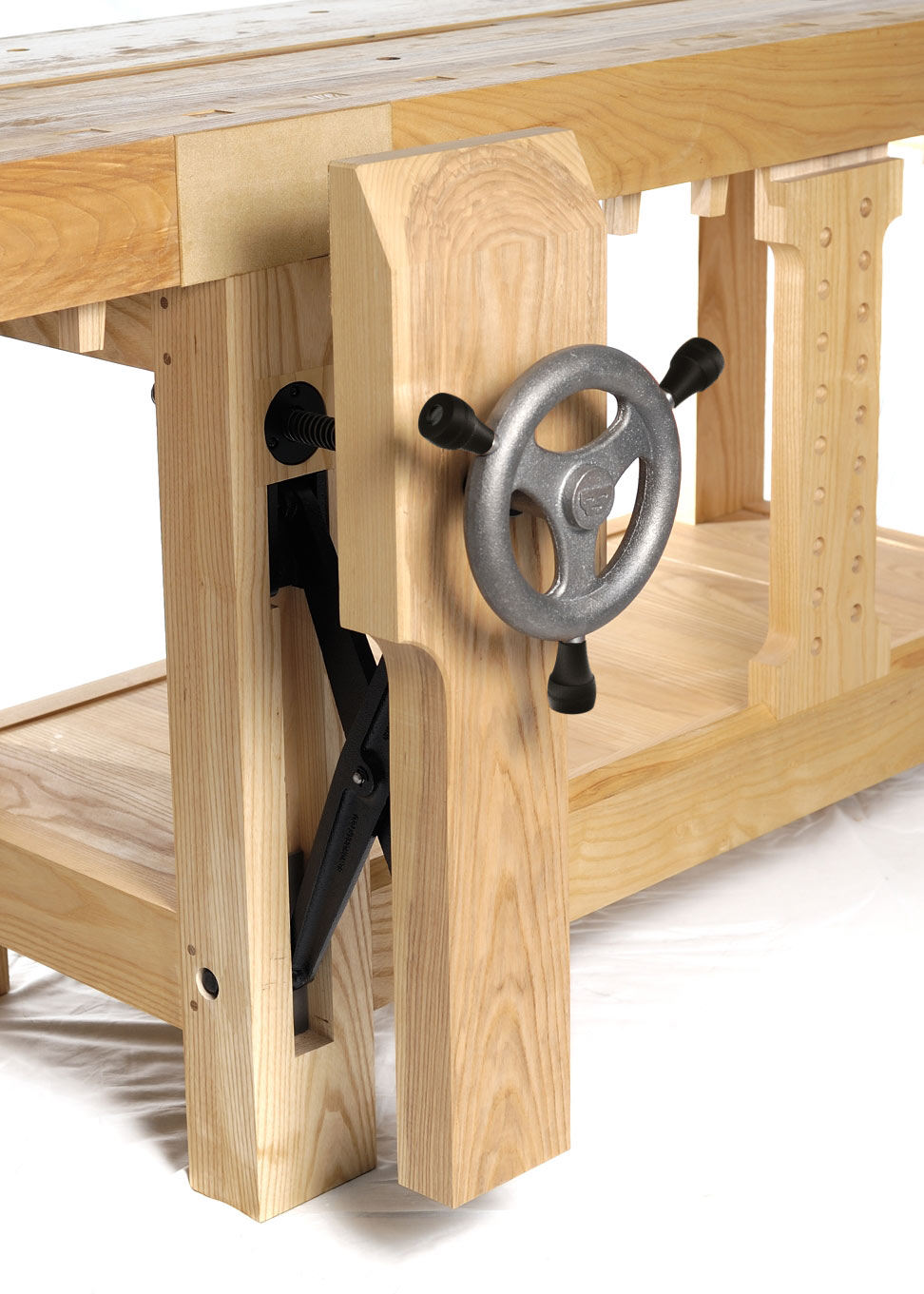
Cast Iron Handwheel
Traditional leg vises use a sliding "tommy bar" to operate the vise. This style of handle offers one distinct advantage: lots of leverage. We've engineered the Glide to deliver rock-solid workholding without the need for the big lever of a tommy bar. The massive handwheel allows you to operate the vise with minimal effort and speed. Acting like a flywheel, the handwheel turns the screw and allows you to rapidly adjust the vise with a quick spin. You can open the vise to full capacity (typically 9") in about 4 seconds. Closing it is just as quick and easy. With three knobs oriented at 120 degrees around the wheel's perimeter, there will always be a knob between the 10:00 and 2:00 position. This makes for very convenient operation. Grabbing a knob and rotating from 2:00 to 10:00 (1/3 revolution) moves the chop over 1/8"; more than enough to remove your workpiece. Operating the vise is fun. Giving the handwheel a healthy spin opens the jaw wider and more quickly (use one of the knobs, or grasp the rim itself) and closing the vise from this position with another healthy spin closes the vise rapidly against your workpiece. In most cases, further tightening of the vise is unnecessary.
We offer two versions of the vise. The Glide M and the Glide C. The Glide M features a refined, fully-machined cast iron handwheel with durable, wrinkle coated, aluminum knobs. With a more traditional look and lower cost, the Glide C features a sand-cast iron handwheel. The natural texture of the sand mold is present on the finished handwheel. All other components of the Glide M and C are identical.
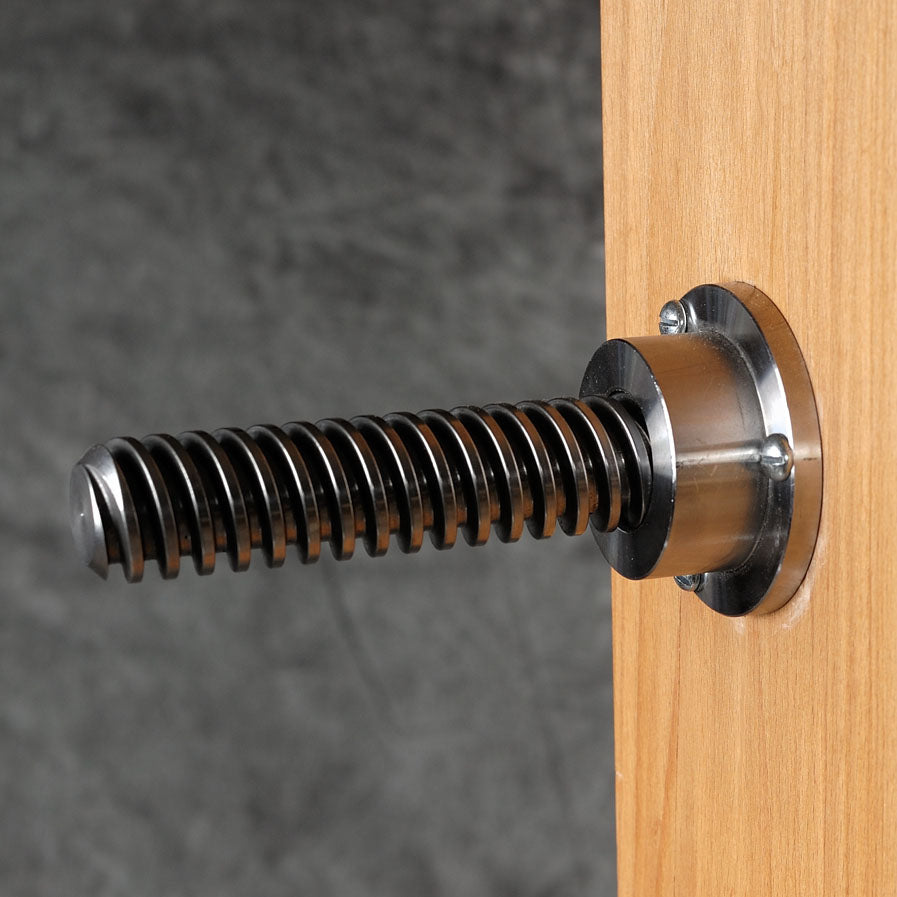
Screw & Nut
The heart of the Glide is a rolled-thread double-lead acme screw. At four turns per inch, the screw opens and closes the chop 1/2" per revolution of the handwheel, twice as fast as typical metal vise screws. Roll threading creates a hardened, polished thread for smooth action, and consolidates the molecular structure for durability, unlike screws with cut threads. We turn our nuts from solid billets of steel and tap them to work sweetly with the Glide's screw.
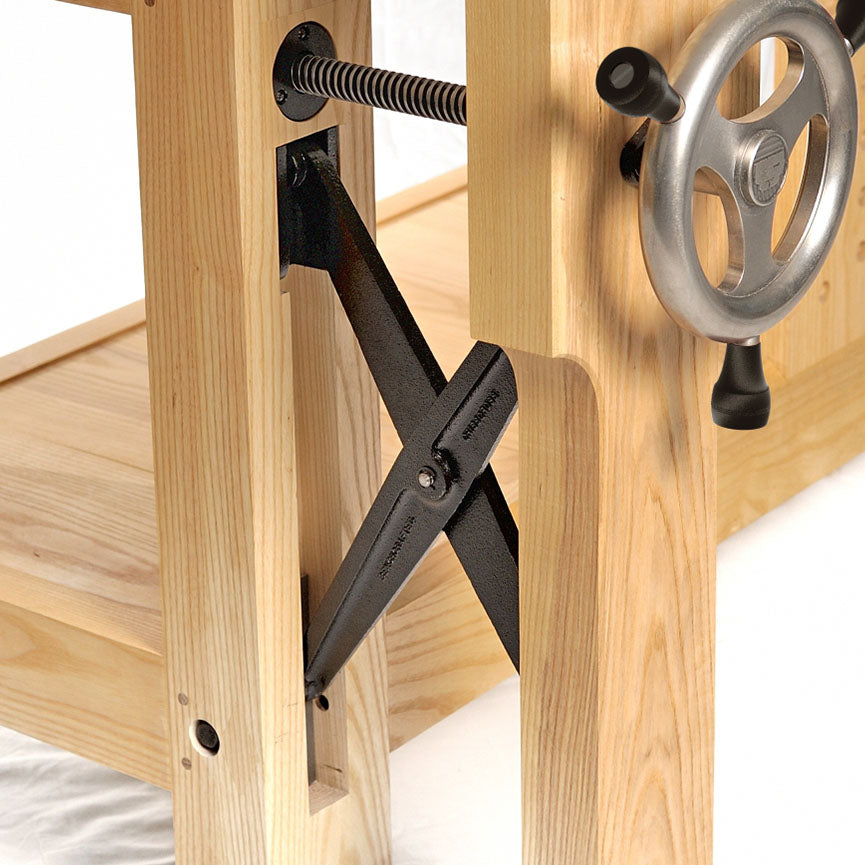
Crisscross
The Benchcrafted Crisscross mechanism is an integral part of the Glide.The mass and free spinning action of the handwheel are provided with unencumbered movement over the vise's entire range by the Crisscross, which completely supports the weight of the chop and Glide components. Additionally, the Crisscross completely eliminates the traditional wooden parallel guide and its adjustment pin. The Crisscross is maintenance free. Once you install it properly, there are no adjustments to make. Ever.
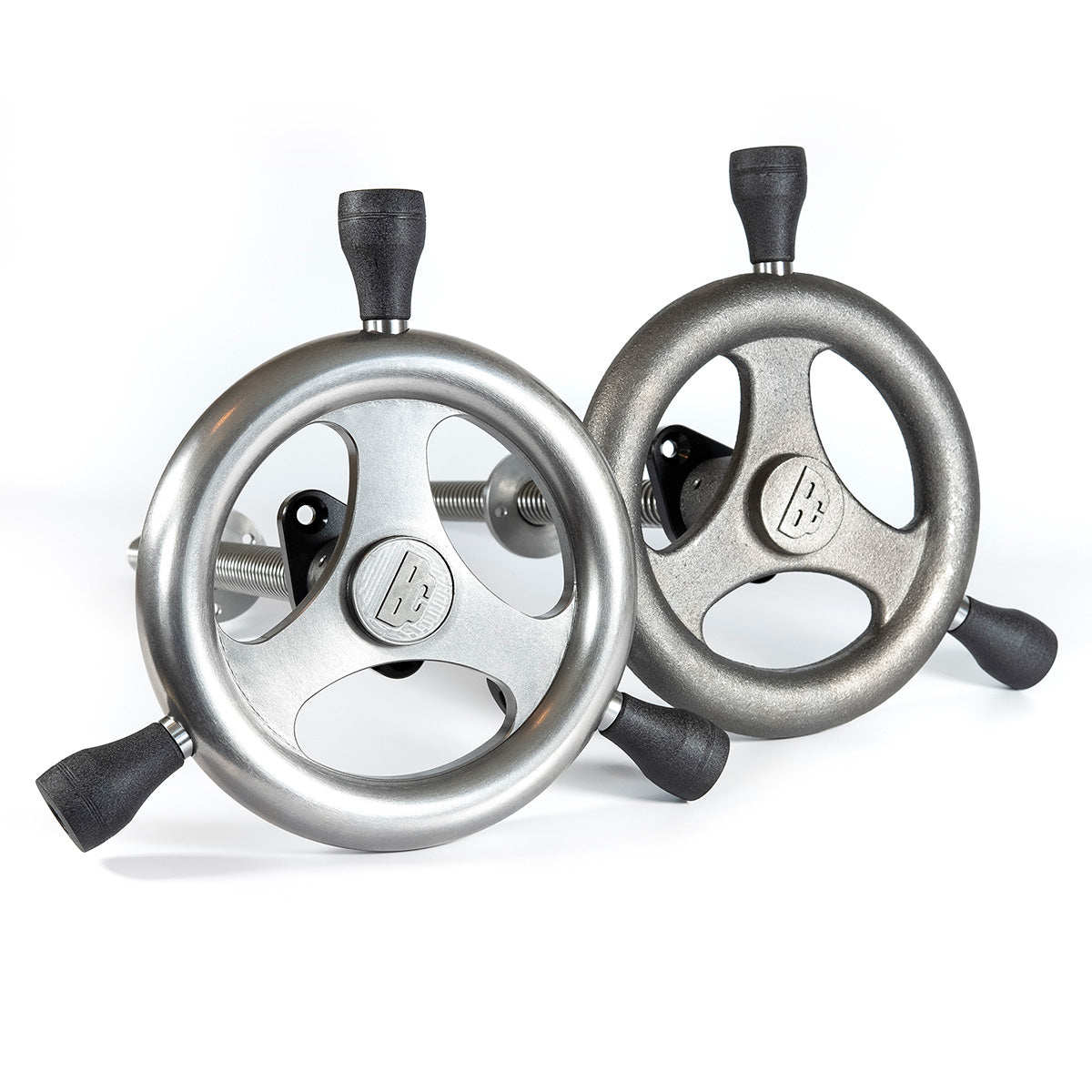
Video
Specifications
Cast and machined from steel components
Designed and made in the USA
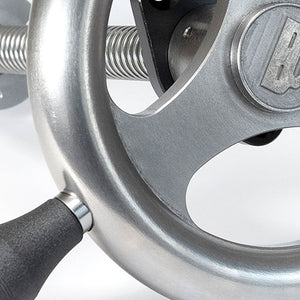
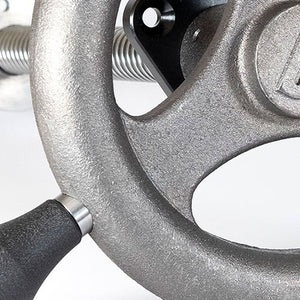
Fully-machined 8" diameter cast-iron hand wheel
8" diameter cast-iron hand wheel
| All Models |
3 satin black, wrinkle coated, aluminum knobs
| All Models |
Includes your choice from our three Crisscross models
| All Models |
Rolled-thread carbon steel double-lead acme screw with 4 tpi pitch for rapid movement & positive clamping pressure - 1/2" travel per revolution.
| All Models |
One-piece acme nut turned and tapped from solid billet cold-rolled steel
| All Models |
3/8" thick steel flange, black oxide finish
Crubber material to line the jaws for a tenacious, non-marring grip
All components needed to build the vise into your workbench
Similar Products